Coil Construction
Issues
1,2,3
The method of construction
used in a coil isn't of much concern if the coilgun is operating under low current
densities. However as the current densities rise the electromagnetic forces acting
on the turns of the coil become very significant. These forces can be large even
without a projectile present. 'Dry firing' a coil will impose a force distribution
on the turns which depends on the magnetic flux distribution. The presence of
a projectile will modify the distribution and the resulting forces. Take a look
at this example of the force which will exist in an energised 'dry' coil. We'll
set up a FEMM simulation with a coil measuring 20mm long x 12mm inside diameter
x 36mm outside diameter. The current density will be set to 1000Amm-2.
Axial Force
Simulation -
If we create a
series of closed integration paths and determine the axial force on this cross
section element we can begin to appreciate how the force is distributed throughout
the coil.
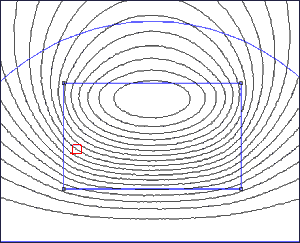
Fig
1. A small closed path used in this simulation.
The
integration path yields the force on a tubular section of the coil as shown in
fig 2. The force is axial because the simulation is axis-symmetric.
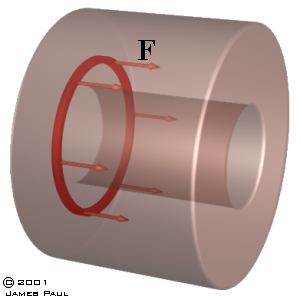
Fig
2. Simulation yields force on a tubular section of the coil
We
only need to generate data for one side of the coil since the system is symmetric
about its midpoint. It will be a different story when a projectile is introduced.
The integration contours form 1mm2 cross sections of the coil so the
axial force represents the force per square mm of wire over a revolution. The
data from this simulation are plotted as a colour map as shown in fig 3 below
(positive force is taken as directed to the right). We'll call this a Type 1 force
map.
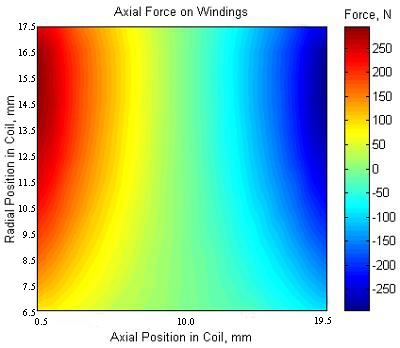
Fig
3. Force distribution on filamentry sections
If
we want to know the actual force experience by a small section of wire we need
to divide the original force values by the circumference of the winding at a given
radius. This will result in the force per mm of circumference per square mm of
cross sectional area (i.e. roughly per cubic mm). We'll call this a Type 2 force
map.
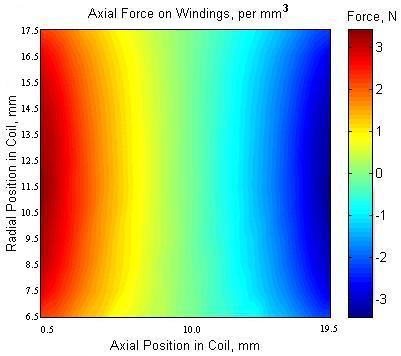
Fig
4. Force distribution on small volume.
You
should notice that the force distribution now shows the peak force to be occurring
around the half thickness of the coil. Notice that the axial force is greatest
at the ends of the coil and its direction is towards the centre of the coil. What
about the radial force?
We'll
now look at how the force distribution changes with a projectile halfway into
the coil. The Type 1 map is shown below.
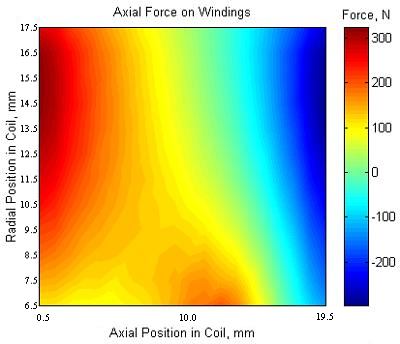
Fig
5. Type 1 map with projectile.
Again
we can plot the data as a Type 2 map.
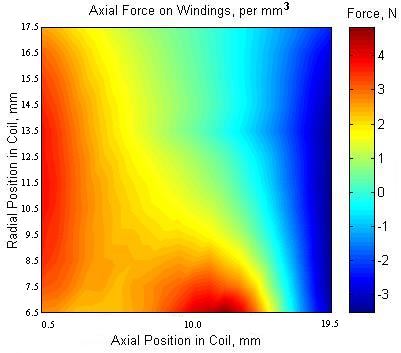
Fig
6. Type 2 map with projectile.
Notice
how the force is particularly intensive at the centre of the coil, in fact the
peak force occurs in a completely different place when the data is viewed in this
way. While this type of simulation is interesting it is very labour intensive,
it takes about 1-11/2 hrs to generate the full array of
data. You may get the impression that there are lots of data points but in fact
the data array is only 20x12. The maps are plotted using interpolation between
the points to give a smoother look.
So
what do we make of this? The Type 1 map may have a practical use since it plots
the force on a position dependent volume. This may be useful in building a stress
model since these models sometimes use distributed loads. The Type 2 map is useful
as it gives us an indication of the force on a fixed volume (cubic mm in this
case) and lets us see where the peak loading will occur. This is important since
this could be the most likely point of mechanical failure.
Note
that these are force maps, not stress maps. In order to determine
the stress distribution we need to use the force values obtained from simulations
like those above and apply them to a mechanical stress simulation model. This
type of simulation needs additional information about the coil properties as well
as which parts are to be considered anchored, i.e. the parts which are fixed.
In the case of the coil, one part which could be considered fixed is bottom of
the first layer of windings - they are fixed to the accelerator tube. However,
if a more accurate analysis is required then we may want to be more realistic
and choose the ends of the tube as the fixed parts. This will allow a more accurate
analysis of the system since it will take into account the properties and deformation
of the tube. It may be possible to directly determine the stress distribution
using a high end package such as Ansys which employs coupled field analysis.
The
stress distribution will probably look very different from the force distribution.
As a quick example, consider a vertical solid cylinder. If we look at any small
volume we find that the force on that volume is simply its mass multiplied by
G with a resulting homogeneous force map. If we now think about the stress we
find that the stress gets larger as we move towards the bottom of the cylinder
due to the cumulative effect of the weight as we move down the column.
Strengthening
the Coil
These
are a few suggestions on what can be done to strengthen a coil. A more detailed
construction methodology requires information on the true stress distributions.
It may be possible to determine this to some extent with Quickfield since the
programme can perform axis-symmetric simulations for mechanical stress.
The
simplest thing which can be done is to impregnate the coil with some sort of resin.
Many industrial coils use vacuum to assist the penetration of the resin, this
isn't really an option for a hobbyist. For minimal hassle the resin can be introduced
after the coil has been wound however the penetration is limited and only works
well for thin resins. Ideally the resin should be applied after each layer is
wound so that it fully permeates the coil. This can be a tedious task since some
resins can take many hours to set. Some possible resins which can be used:
Acrylic
spray - The stuff used to seal circuit boards. This has the advantage of being
quite 'runny' and seeps into the windings without much trouble. It's not particularly
strong but it does offer good protection against moisture.
Epoxy
Resin - This comes in a multitude of different varieties. The most
suitable types are those with a long setting time. These take several
hours to cure and this allows the resin to penetrate the windings
more fully. It is possible to thin epoxy with cellulose thinners
but you need to make sure that the wire insulation isn't affected
by the thinner. The last thing you want is for the finished coil
to be ruined by internal short circuits. A faster setting epoxy
can be used if it is applied as the coil is wound. This ensures
that all the turns are coated but it is a tedious task.
For
a really strong coil it is necessary to bind the layers with something
like glass fibre or carbon fibre reinforcement. The coil then undergoes
vacuum impregnation to fill all voids with resin. Based on the simulation
above I'd say that simply impregnating the coil with resin is sufficient
to strengthen it for most coilgun applications.
There is a brief description of high strength coil manufacture at
the National High Magnet Field
Laboratory. See also Principles of Pulsed Magnet Design
for a detailed presentation on the theoretical analysis of stress
in pulsed coils.
In
the next section we'll look at the radial force acting on the windings.
Last
Modified: 12 Feb 2004
|