Current Sensor
Module
In
order to measure the current we need some sort of current sensor,
which can simply be just a short section of wire inserted into the
current path. The wire resistance needs to be small compared to
the circuit resistance so that the measurements don't alter the
behaviour of the system. Since many coilgun circuits have resistances
of the order of 1
and run currents of 100A or more, a suitable sensor should have
a resistance of say 0.01
or 1% of the circuit resistance. In this case the sensitivity will
be 10mV/A. Something to note is that although the power dissipation
would be around 100W at 100A you don't need a high rated resistor
since the event time is of the order of a few ms. You're not going
to easily find a 0.01
resistor but you could wire up several low value resistors in parallel
to drop the resistance. Alternatively you could make one using a
piece of enamelled wire. What you need to do is decide on the resistance
of the sensor then pick a sensible wire diameter, between 1 and
2mm is a safe bet. Now you can work out the required wire length
using the resistance formula -
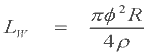
Here
LW works out as 722 mm using a 1.25 mm diameter wire (resistivity of
copper is 1.7x10e-5 mm).
It's best to wrap up the wire so as to minimise its inductance. You can do this
by wrapping it back and fourth as shown below. Note that there is an inherent
inductance in any conductor - even a straight wire. This arises due to the flux
which exists inside the wire (this gives rise to the skin effect) and is independent
of the diameter of the wire. The value of the internal inductance is 5e-8H/m which
is insignificant compared to typical coil inductances of several uH.
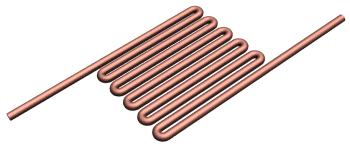
Fig
1. Flat winding
Alternatively,
you could wrap the wire so that the turns are wound in alternate directions. This
does have quite a lot of inductance compared to other winding configurations so
it is best used for low frequencies, if at all.
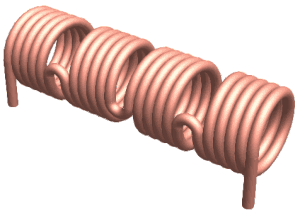
Fig
2. Opposing winding
The
current sensor module is wound with 1.25mm wire, with the current
terminals made from brass. The sensor voltage is brought out to
a screw-less terminal block.
Fig
3. Current Sensor Parts
Fig
4. Completed Current Sensor
After
several attempts at getting the winding length correct the accuracy of the sensitivity
is better than +/- 2%. The inductance is less than 1uH.
Version
2:
I
made this sensor using constantan resistance wire so that the wire length and
inductance would be minimal.
Fig 5. Constantan element sensor.
The
accuracy of the sensitivity is better than +/- 2%. The inductance
is primarily internal inductance and so it is irrelevant unless
the frequency of the current approaches several hundred MHz. The
limiting factor with this sensor is the skin effect which causes
more charge to flow close to the outer surface of the wire than
in the bulk of the conductor - the resistance is frequency dependant.
This sensor consists of several strands of wire to reduce the skin
effect but the useful frequency range is still limited to about
400kHz.
Version
3:
This
sensor design is based on a commercially available 0.01
resistive element. The element is reshaped to reduce inductance
and a coaxial lead is soldered directly onto the ends of the element.
Fig 6 shows the completed sensor with BNC terminated coaxial lead.
Fig 7 is a close up of the sensor element. Note the thin red plastic
strip separating the opposing sides of the element.
Fig
6.
Fig
7. Sensor element with plastic seperator strip.
|