Inductance Calculation
Technique
This
technique is presented in the FEMM manual, and offers a means of
determining the inductance of any generalised axisymmetric coil
geometry.
The
first thing to do is to define the coil geometry in the FEMM problem
editor. Fig 1 shows a simple rectangular coil whose dimensions are;
L_=_27
mm, Ro_=_18
mm, Ri_=_7
mm.
The
outer boundary of the problem is given a Mixed boundary condition
such that the field lines are properly 'formed' when they meet the
boundary. This procedure is detailed in the FEMM manual. Materials
are also assigned to the relevent regions. Most common materials
are available from the FEMM materials library. The 'Coil' material
is a renamed copy of the Copper material from the library.
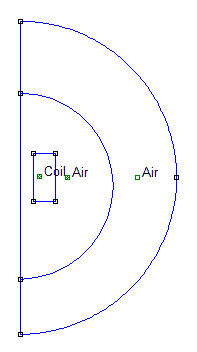
Fig 1. Problem geometry.
The
particular value of the Coil source current density isn't important,
but the equivalent wire current value that would produce this needs
to be calculated later on. Filling factor values depend on the neatness
of the winding as well as on the insulation thickness of the wire.
A value of 0.7 is assumed for the filling factor.
After
setting all the problem parerameters the geometry can be meshed
and then solved. The resulting field pattern is shown in fig 2.
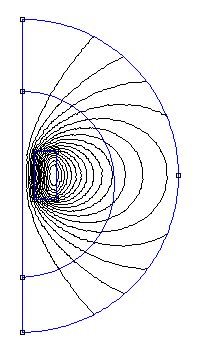
Fig 2. FEMM view plot of the field
pattern.
In
order to determine the self inductance we need to calculate the
A.J integral for the coil: Simply select the area selection tool
and click on the coil region which should then turn green. Now select
the A.J option from the Block Integrals dialog. The resulting A.J
value for this coil is 1.009606e-3 Henry Amp2. Now the
equation relating the inductance to the coil current is:
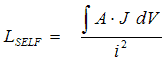
so
the last thing we need to know is what i value to use. Going back
to the Coil properties dialog we note that the value of J is 1 MA/m2.
The diameter of the wire used in the coil is 1.8 mm so the current
carried by the wire is:
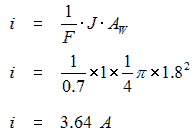
Therefore
the self inductance of the coil is:
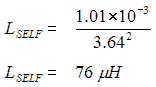
We
can look at the actual RL response of the coil by applying a step
voltage to it via a resistor, and then determine the time constant
and hence inductance from the exponential waveform. Another possibility
is to discharge a small capacitor into the coil and determine the
inductance from the resulting ring down oscillation. In this case
the coil, switch, and wiring resistances are ignored, which is valid
as long as the damping factor is small (the resistance affects the
damping factor which is a variable in the inductance calculation).
Table 1 gives the results of the various measurements.
Method |
RL
(R=18) |
RL
(R=2.7) |
LC
(C=100n) |
LC
(C=2.2u) |
LC
(C=11u) |
Inductance |
50
uH |
66
uH |
47
uH |
62
uH |
69
uH |
Equivalent
f |
56
kHz |
8.1
kHz |
74
kHz |
14
kHz |
5.8
kHz |
Table
1. Inductance values obtained from different measurements.
Clearly
there is a discrepancy between the FEMM-derived value and the measured
values, as well as variations within the measured values. This is
attributable to the frequency dependent behaviour of the coil -
the values are closer to the calculated value when the waveform
is slower, be it an exponential or a damped oscillation.
If
we think of a coilgun current pulse as approximating a half-sine
shape, then the equivalent frequency based on very fast pulse duration
of 100 us is 5 kHz. It would appear then that the steady state inductance
value derived from the FEMM analysis can be taken as a reasonable
indication of the coil inductance under coilgun conditions. Uncertainty
about the filling factor will affect the accuracy of the FEMM-derived
value.
For
an analysis of the high frequency behaviour of inductors see for
example -
A.
Massarini, M.K. Kasimierczuk, and G. Grandi, "Lumped Parameter
Models for Single and Multiple-Layer Inductors"
|