Metallic Tubes
The use of a metallic
accelerator tube is great in terms of strength but it suffers from a major drawback
- induced eddy currents. The problem is not a trivial one, it places severe limitations
on the muzzle velocity of the projectile. There are things which can be done to
reduce the effect. Firstly we need to try and visualise how these currents exist
within the accelerator. If we set up a FEMM simulation and plot the flux distribution
along a contour representing a section of accelerator tube as shown below, we
can get an idea of the flux distribution. This will allows us to begin to determine
how the flux changes as the projectile moves along the accelerator. The simulation
is a simple setup with a coil current density of 50MA/m2 (50A/mm2)
and a silicon steel projectile.
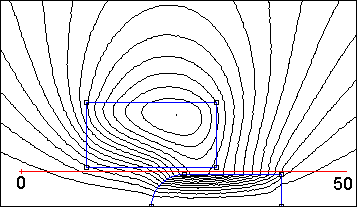
Here
we have the field line plot of the solution to this simulation, the integration
contour is situated halfway between the coil and projectile and spans 50mm. Various
quantities can be plotted but we are interested in magnetic flux density.
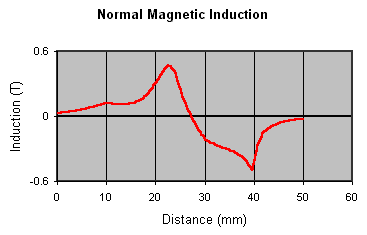
This
is a graph of magnetic induction (flux density) normal to the integration
path. The normal component is responsible for driving the circumferential eddy
currents. This shows that the flux is significant over the length of accelerator
tube bounded by the coil and projectile, in this case between 10mm and 40mm. The
flux density falls off fairly quickly either side of this boundary.
Two examples of
slotted accelerators are given below. The stainless steel accelerator had slots cut by machining
across the tube, this was done using a milling machine. A file could have been
used to achieve the same end but it would take a much longer, particularly
on a tougher material like stainless. The brass accelerator slots were again cut with
a milling machine, in this case a small diameter mill was plunged into the tube
and drawn along it to cut each slot. This is a faster method, especially on a
thin tube and a softer metal. On a practical note, there is a lot of work needed
after the machining to remove burr from the edges of the slots. A needle file
set is invaluable for working in thin slots. Cleanly machined slots are essential
for a smooth operation, in fact a projectile can easily get jammed if there are
any rough edges left.
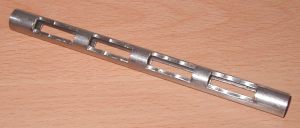 |
This stainless
steel accelerator tube is 12.7mm OD with a 1.6mm wall thickness. The projectile
must be a good fit in the tube if the slots are wide, otherwise it will attempt
to 'fall out' of the slot and ram up against the end of the slot as it moves forward.
I machined this
brass tube as a practice exercise, it isn't used for any practical experimentation
There are four rows of slots arranged around the circumference, the slots are
also offset axially to further reduce eddy current paths. The OD is 12.7mm and
the wall thickness is 0.8mm. Brass machines very easily compared to stainless.
Note that slotting
the tube DOES NOT completely eliminate eddy currents. Consider a tube with a full
length slot as shown in fig 5 (ok it's not strictly a tube anymore).
Fig 5. Full length slotted tube.
If we pass a time
varying current through the coil it will generate a time varying magnetic field.
This field (or induction) has an associated electric field that can drive currents
in any conductors through which the field penetrates. Since the tube has a finite
thickness there remains a closed path around which eddy currents can travel. Fig
6 shows the tube end-on with the current path travelling around the outer surfaces
of the tube.
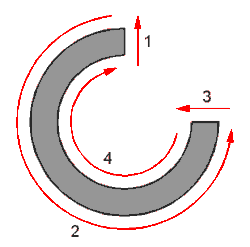
Fig
6. Eddy current path.
Although
eddy currents can still occur in the tube their magnitude is much smaller because
the cross-sectional area of flux enclosed by the tube surfaces is greatly reduced
- the electric field associated with the flux through the bore no longer has a
closed path around the tube.
A
theoretical treatment of eddy currents can be found in -
Eddy
Currents: Theory and Applications, Proceedings of the IEEE, VOL. 80, NO. 10, OCTOBER
1992
|