Projectile Design
The projectile
has as much influence on the performance of a coilgun as any other major subsystem.
If we want to design a 'good' projectile then we need to look at reducing or eliminating
eddy currents, picking the best material B-H properties, surfacing or skinning
the projectile for minimum friction and shape profiling for minimum aerodynamic
drag.
1. Projectile
Eddy Currents -
If we take a solid
ferromagnetic projectile and fire it through a coil then it will experience a
highly dynamic magnetic flux. The currents induced by this flux will generate
an opposing flux and the net accelerating force on the projectile will be reduced.
The penetration of the magnetic field is also limited and so the projectile experiences
a reduced bulk magnetisation. The problem becomes more and more significant as
the speed increases and the switching times are reduced so if the projectile is
intended for a high speed coilgun then steps should be taken to reduce the eddy
currents. Two different approaches can be taken, slotting the projectile or powdering
it.
2. Slotted Projectile
-
Slotting the projectile
restricts the ability of the eddy currents to flow in the material. The direction
of the slotting should be axial since we are more interested in stopping circumferential
eddy currents. Obviously slotting will reduce the mechanical strength so progressive
depth slotting is a means of reducing this. One possible design is shown below.
3. Powdered
Matrix Projectile -
An alternative
approach is to powder the material and bond it together in a resin matrix. This
eliminates eddy currents in all possible directions. The cutaway below shows a
bonded matrix projectile with a plastic jacket. This has two advantages, firstly
the material can be poured into the jacket like a moulding making fabrication
easy and secondly the plastic will readily engage rifling if spin stabilisation
is required. One disadvantage of a PMP is that it has to carry the matrix material
as baggage which doesn't contribute to the force on the projectile. Bearing this
in mind it makes sense to compress the powdered cored material as much as possible
so that excess bonding resin is removed.
Fig
3.1 Powdered matrix and slotted projectiles
4. Projectile
Shape -
What
effect does the shape of the projectile have on the force curve and the resulting
energy transfer? We can answer this by doing a series of FEMM simulations for
various projectile shapes starting with a plain rectangular cross-section, then
progressing through rounded nose profiles to a sleek profile with a sharp sweeping
nose.
5.
Aerodynamic Drag - Subsonic Speeds
It's
quite surprising to realise just how much influence the shape of the projectile
can have on its aerodynamic properties. The drag on a projectile can be seperated
into two distinc types - form drag and skin friction.
Form
Drag -
Form
drag results from the generation of vortices as the projectile displaces the air
around it. Fig 5.1 illustrates this.
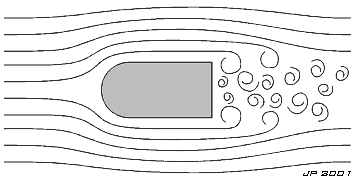
Fig
5.1 Induced vortices
The
formation of vortices requires energy and this comes from the kinetic energy of
the projectile. The vortices eventually dissipate behind the projectile and the
streamlines return to a smooth profile. In order to minimise the form drag the
projectile needs to be 'streamlined'. The best general streamlined shape is shown
in fig 5.2.
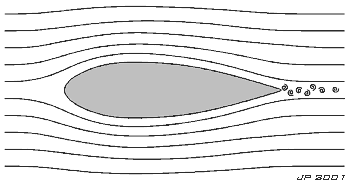
Fig
5.2 Highly streamlined body
The
length/diameter ratio of such a body is termed its 'fineness ratio'. Form
drag is minimised when the fineness ration lies between 3 and 4. While this shape
might provide minimal form drag it is not a good shape for running down an accelerator
tube - it is likely to wobble and possibly jam. Some sort of tail end support
could cure this. Fig 5.3 shows fin type supports. These would also provide some
flight stabilisation but I'll look at this later.
Fig
5.3 Fin supports guide projectile in accelerator tube.
This
shape resembles a sort of WW2 drop bomb or a hot air blimp. The addition of fins
will increase the form drag somewhat so this design of the projectile would be
a compromise between practical functionality and aerodynamic performance. Note
that three fins is the minimal number necessary to support the tail end in a plain
tube however if the tube is slotted then more fins will be needed to fully support
the end in all rotational orientations. Another possibility is to use a tubular
'aerofoil' type fin at the end as illustrated in fig 5.4.
Fig
5.4 Tubular fin arrangement
This
type of tail support will be able to run through a tube with any slotting arrangement.
Whether this will adversely affect the aerodynamics depends on the shape of the
joint area between the fins and the projectile body as well as the shape of the
leading and trailing edges of the fins.
|