Switching Devices
There are several
broad categories of switching device available as listed below. The benefits and
drawbacks of each type will be discussed briefly.
1. Thyristor
(SCR)
The thyristor is
a three terminal device consisting of an anode, cathode and gate.
The circuit symbol is shown below.
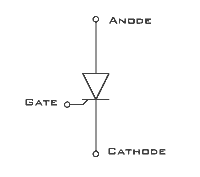
Fig
1.1
When there is no
gate current the device is in the non-conducting state and will hold off positive
and negative bias voltages. The zero gate current characteristic is:
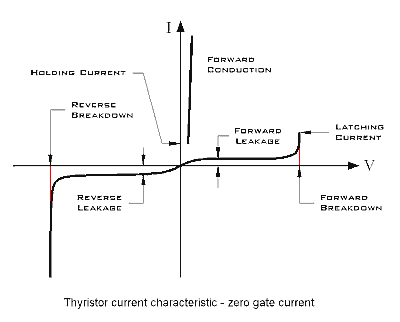
Fig
1.2
If gate current
is now injected into a positively biased device it will begin conducting current.
Once the threshold latching current level is achieved the gate current can be
removed and conduction will continue. The device will remain on until the anode
current is reduced below the the holding current. The latching current and holding
current levels are not the same.
This is the device
of choice when using a basic capacitor discharge coilgun. The thyristor will hold
off the capacitor voltage until it is triggered into the forward conduction zone
by the gate current signal. The capacitor then discharges through the thyristor
into the coil and the current decays to zero. There is no option for turning off
the the current once the device is conducting.
2. Bipolar Transistor:
NPN
This device operates
as a current amplifier. It consists of three terminals, the Base, Emitter
and Collector. Its circuit symbol is shown below.
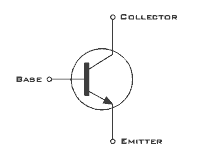
Fig
2.1
The device amplifies
the current into the base terminal by allowing a much larger current to pass from
the collector to the emitter. This gain varies between transistor types ranging
from several hundred for small signal transistors to a few tens for high current
power transistors. When used as a switching device the bipolar transistor is operated
in saturation mode as shown below.
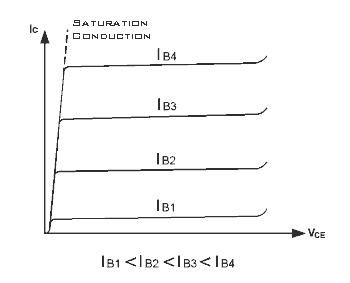
Fig
2.2
When
the device is saturated the voltage drop across the collector and
emitter is minimised, and consequently so are the conduction losses.
You need to supply a large enough base current to ensure the device
will be saturated at the required collector current.
While bipolar power
transistors offer high current capacity they require substantial base drive current
(as much as 10% of the collector current in some cases) and this requires additional
signal processing from the control system.
3. Power MOSFET:
N-Channel Enhancement Mode
The MOSFET is a
three terminal device consisting of a source, drain and gate.
The symbol is:
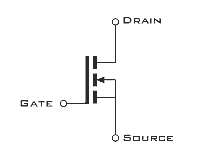
Fig
3.1
The current is
controlled by the gate-source voltage level. A typical threshold voltage is around
2-3V above which the device begins to conduct. The diagram below shows typical
current curves for various gate-source voltage levels.
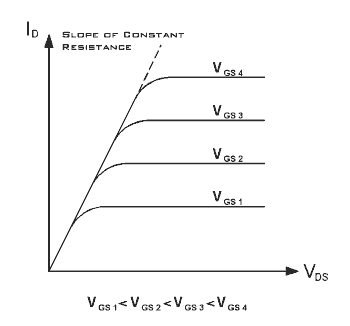
Fig
3.2
This graph shows
that the MOSFET behaves as a plain resistance over a certain range of drain-source
voltages. The gate-source voltage controls the limit on the conduction current.
For the purposes of simply current switching, the MOSFET should be operated within
the constant resistance region. This means that for maximum current capacity the
gate-source voltage should be pulsed at the correct value. If you take a look
at a typical power MOSFET data sheet you'll find a set of current curves like
those above. At higher gate-source and drain-source voltages the current has a
more complicated characteristic.
4. Insulated
Gate Bipolar Transistor
This
device offers the ease of control of the MOSFET with the higher
current capacity of the bipolar transistor. The IGBT does require
a slightly higher gate voltage to ensure that it is fully turned
on. IGBTs are more difficult to operate in parallel due to their
negative temperature coefficient.
5. Semiconductor
Thermal Issues -
All devices have
some form of conduction resistance and this leads to the generation of heat when
the device is in operation. The ability to dissipate the heat is one of the major
factors determining the operational voltage and current capacities of a device.
The manufacturers of devices and heatsinks provide data about their dissipation
capabilities and these allow us to correctly select components.
The
flow of heat starts at the semiconductor junction through which
the current travels. Heat is conducted through to the device body
to the casing surface and then to the air. If the device is fixed
to a heatsink then there are two additional stages in the heat flow
path. In order for the heat to flow there must be a temperature
difference between each stage. We define the thermal resistance
of a heat conduction stage by the ratio of the temperature difference
and the power dissipation as shown below.
Lets
look at the simple situation where we have a device with the following parameters:
On resistance |
0.04 |
|
Maximum continuous current |
30 |
A
|
Maximum junction temperature |
175 |
0C
|
Thermal resistance, Junction -> Case |
2.0
|
0C/W
|
Thermal resistance, Junction -> Ambient |
75
|
0C/W
|
Maximum dissipation |
80
|
W
|
Ambient air temperature |
25
|
0C
|
Table
5.1
We
can use this data to calculate the maximum dissipation from the device operating
without a heatsink Rearranging the eqn 5.1 for P and solving gives us
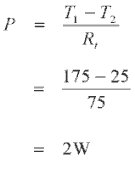
At
this level of dissipation the continuous current would be restricted to 7A. Clearly
the operation of the device is severely limited without the use of a heatsink.
Suppose we want to run the device at its maximum continuous current, how do we
select an appropriate heatsink?
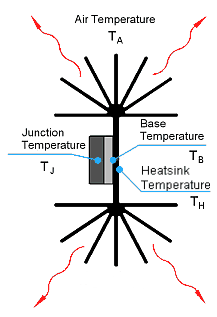
Fig
5.1
Firstly
we need to examine the thermal resistance of a series of linked components. The
diagram below shows the relationship between the thermal resistances and the temperatures
at the interfaces.

Fig
5.2
The
flow of heat through the various stages can be represented as a series connection
of thermal resistances. What might not be so obvious is the value of the base
to heatsink thermal resistance, RBH. This depends on the method used
to fix the device to the heatsink. For most low voltage applications using a single
device, simply bolting it directly onto the 'sink with some heat transfer compound
smeared between the mating surfaces is fine. A typical value for the thermal conductivity
of a heat transfer compound is around 1 W/mK (watts per metre - kelvin). To find
a thermal resistance for this interface we need to take a closer look.
Fig
5.3
Power
dissipation is related to the physical parameters by the formula
where
k is the thermal conductivity, A is the interface area, T2 is the low
temperature, T1 is the high temperature and x12 is the thickness
of the interface layer.
We
can equate this to the thermal resistance formula above to get
Now
the thickness of the heat conducting layer is of the order of say, 10um, the length
and width of the package base is 15mm and 10mm respectively (we'll ignore the
hole in the tab) so plugging these values into the eqn 5.3 gives us
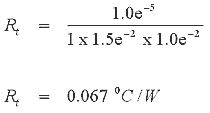
This
is a very small thermal resistance and it's not surprising considering the wafer-thin
layer of compound between the base and the heatsink. In many cases it's probably
safe to ignore this completely. There are other methods of fixing devices to heatsinks
which provide high electrical insulation by using a thin plastic backing piece
and in these instances, the thermal resistance will more than likely need to be
considered.
Finally
we can calculate the required heatsink thermal resistance as follows.
Since the total
thermal resistance is just the sum of the individual resistances we can write
The
power dissipation will be 36W so plugging in the values we get
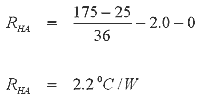
This
requires a fairly meaty heatsink! Go look up a heatsink with this
thermal resistance and you'll see what I mean.
These
issues are further complicated by the fact that the device resistance
changes with junction temperature. Data sheets now tend to carry
two current ratings for the device; one for 25 0C, and
the other for 100 0C. The latter is a more realistic
value to use when selecting a device.
6.
Pulsed Switching Issues-
In
pulsed switching applications such as the coilgun the switching
and conduction losses determine the maximum operating current and
voltage levels. The safe operating area, as defined in the device
data sheet, details the current and voltage boundaries which will
not damage the device. Fig 6.1 shows a typical Safe Operating Area
characteristic.
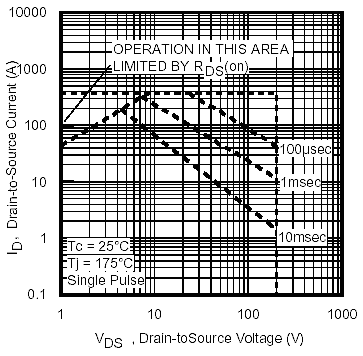
Fig
6.1 IRFP90N20D Safe Operating Area
One
thing which you should note is that the drain-source voltage limits are much more
restricted at higher currents. The limiting slope on the left side of the graph
is due to the devices resistance - the current rises linearly with the voltage.
Dissipation within the device places an upper limit on the constant voltage and
current that the device can handle.
7.
Inductive Switching Issues-
The
switching of inductive loads can be very hazardous for the health
of the switching device. While mechanical switches can cope with
the arcing between the contacts at the expense of operating life,
a semiconductor device will almost certainly be killed by the large
voltage transient at turn off. The simplest method to solve this
problem is to use a commutating or clamp diode across the inductive
component. The diagram below shows the layout of a diode clamped
coil with MOSFET switch.
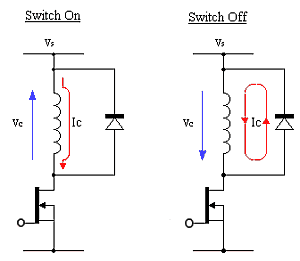
Fig
7.1
When
the switch is conducting, the diode is reverse biased and therefore
no current exists in the diode branch. If the MOSFET is turned off
quickly, the collapsing magnetic flux of the coil induces a voltage
in the coil which tries to maintain the current. The faster the
current is switched off, the larger is the induced voltage. Without
a commutating diode the induced voltage could reach several hundreds
or even thousands of volts - certain death for the MOSFET if the
pulse exceeds the rated avalanche energy. Basically the commutating
diode provides a low resistance path for the induced voltage to
drive the current. The voltage only needs to rise enough to reach
the conducting voltage of the diode, usually around 1V. This keeps
the MOSFET happy and ready to fire another projectile.
While
this is certainly an effective means of limiting the turn off transient
voltage, it isn't necessarily the best in terms of turn off speed.
Ideally we want the current in the coil to turn off as quickly as
possible. The simple commutating diode is far from this goal. If
we want the current to decay faster we need to let the induced voltage
reach a higher value. The absolute maximum we can allow it to rise
depends on the voltage rating of the device. Suppose we are using
a 60V MOSFET and a 40V supply, the largest induced voltage allowable
is then 20V. One possibility is to connect a resistor in series
with the diode. The specific value would need to be determine according
to the coil current at turn off, the supply voltage, and the maximum
device voltage. Another would be to use a zener voltage clamp across
the MOSFET There is a whole area of semiconductor power electronics
which deals with switching issues, the circuits are usually termed
'snubber' circuits.
|