Three
Stage Induced Voltage Triggered Coilgun
Following
on from the development of a single stage induced voltage triggering
system, this experiment combines several deta-peak triggers for
use in a multistage configuration. The details of the construction
of the 3-stage accelerator are illustrated in figs 1a through 1j.
|
|
|
Fig
1a. Stainless steel tube with slots, and ribbed zones for
fixing end formers. |
Fig
1b. Sensor coil former made from nylon 66. |
Fig
1c. Drive coil former with recess and wire exit slot. This
piece is made from acetal. |
|
|
|
Fig
1d. Trial assembly of parts. |
Fig
1e. Sensor coil wound with approx 100 turns of 0.2 mm wire. |
Fig
1f. Sensor coil glued in place with epoxy resin. |
|
|
|
Fig
1g. Output wires are soldered in place. |
Fig
1h. Remaining void is filled with epoxy resin.
|
Fig
1i. Formers are fitted and paper insulation is wrapped onto
tube to protect the drive coil insulation. |
|
|
|
|
Fig
1j. Drive coils are wound and terminated with 3 mm eyelets.
The winding method is illustrated on this page. |
|
The
multistage system operates in a cascading fashion. The sequence
is activated by the triggering of stage 1 via a manual switch that
sets the delta peak trigger 1 drive signal high. This primes the
input to the second stage but does not yet trigger it. Sensor 1
detects the passage of the projectile setting the stage 1 drive
signal low. This falling edge triggers the second stage, setting
the drive signal high and priming the input to the third stage,
and so on. The connectivity of these signal paths is illustrated
in figure 2. A disadvantage of this system is that should a triggering
event be corrupted in some way the sequence will likely stop. This
is in contrast to an optically triggered multistage system where
each stage operates independently.
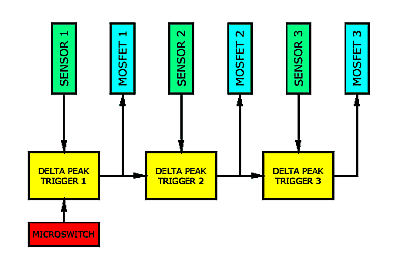
Fig
2. Signal paths required to provide cascading behaviour.
The
key timing events are shown in fig 3. The sequence is as follows:
- Manual
switch is pressed setting the output of stage 1 high
- Delta-peak
trigger 1 sets the output of stage 1 low
- The
falling edge on the stage 1 output triggers stage 2 setting it's
output high
- Delta-peak
trigger 2 sets the output of stage 2 low
- The
falling edge on the stage 2 output triggers stage 3 setting it's
output high
- Delta-peak
trigger 3 sets the output of stage 3 low, completing the sequence
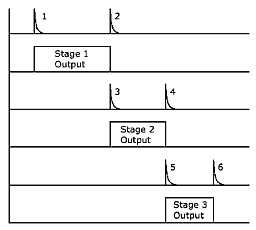
Figure
3. Timing events as seen on the CLK pins and the Q output.
The
trigger design for stages 2 and 3 differs only slightly from that
used in stage 1. Referring to figure 4 we can see that the drain
and source of a small MOSFET are connected across the sensor signal
input with the gate of this device being driven by the 'Q-bar' or
'NOT-Q' output of the flip-flop through a signal diode. A small
capacitor and resistor are connected in parallel with the gate and
source of the MOSFET which creates a delay in turn off when Q-bar
goes low. Since Q-bar is high when the stage is idle the sensor
voltage is held low until shortly after the stage is triggered.
This is necessary in order to prevent the delta-peak trigger from
detecting the flux swings from the previous stage.
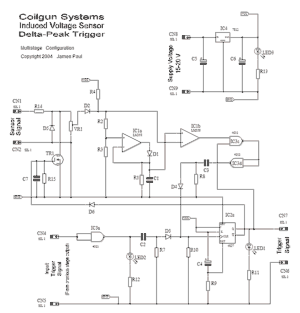
Fig
4. Multistage configuration for delta peak trigger.
In
order for the triggering to follow a cascading pattern each successive
stage needs to be triggered by the falling edge of the output trigger
pulse from the previous stage. To do this the input trigger signal
is inverted via a NOT gate (made from a NAND gate) and then capacitively
coupled to the CLK pin of the flip-flop. When the stage is idle
the input is low and the output of the NOT gate is high, so there
is charge stored in C2. When the trigger input goes high the output
of the NOT gate goes low and C2 discharges through R7 thereby priming
the input. When the input goes low again the rising edge on the
output of the NOT gate produces a pulse on the CLK input of the
flip flop, setting the trigger output high.
Note
that R2 has been increased in value from 150
to 330 .
This was necessary due to a triggering glitch caused by magnetically
induced voltages upsetting the bias voltages of the delta-peak op
amps. Figure 4 shows a glitch. The initial pulse on the CLK pin,
which causes Q to go high, is quickly followed by a second glitch
pulse that shuts off the stage prematurely.
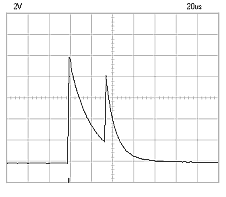
Fig
4. Glitch pulse on CLK pin caused by voltage disturbances on the
delta peak op amp inputs.
Figure
5a shows an example of the capacitor current for three actively
fired stages. The current is measured by a 10 m
resistive sensor inserted at a common return node from the source
terminals of the MOSFET switches, as illustrated in figure 5b.
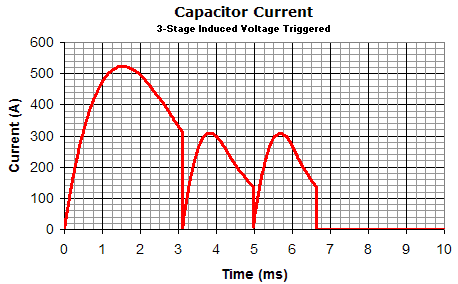
Figure
5a. Capacitor discharge currents.
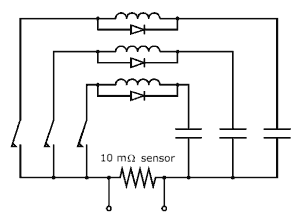
Figure
5b. Current sensor location.
Some
basic velocity and efficiency data for various charging voltages
is shown in table 1. It is interesting to note the increase in efficiency
of the second and third stages when the higher charging voltage
is used. One possible reason for this is that, with the faster projectile
velocity, the current peak may more closely coincide with the maximum
force position of the projectile as it penetrates the coil. This
would naturally result in a more effective transfer of energy to
the projectile.
Launch
Delta = 0 |
Stage
1 |
Stage
2 |
Stage
3 |
Overall |
Capacitance
(uF) |
33,000 |
6,800 |
6,800 |
46,600 |
Charging
Voltage (V) = 40
|
Stored
Energy / Used (J) |
26.4
/ 25.7 |
5.44
/ 5.30 |
5.44
/ 5.34 |
37.3
/ 36.3 |
Velocity
Gain (ms-1) |
14.0 |
1.87 |
1.67 |
17.5 |
Kinetic
Energy Gain (J) |
1.30 |
0.38 |
0.36 |
2.04 |
Efficiency
(%) |
4.92 |
7.17 |
6.74 |
5.62 |
Charging
Voltage (V) = 60
|
Stored
Energy / Used (J) |
59.4
/ 53.4 |
12.2
/ 11.6 |
12.2
/ 11.7 |
83.8
/ 76.7 |
Velocity
Gain (ms-1) |
18.5 |
4.80 |
3.72 |
27.0 |
Kinetic
Energy Gain (J) |
2.28 |
1.33 |
1.24 |
4.85 |
Efficiency
(%) |
4.27 |
11.5 |
10.6 |
6.32 |
Table
1. 3-Stage coilgun performance data using induced voltage triggering.
Conclusions
An
induced voltage triggered multistage coilgun can be implemented
using a slightly modified version of the single stage delta-peak
trigger system. The degree of sensitivity of the delta-peak circuitry
can lead to triggering glitches if the circuitry is in close proximity
to the drive coils. Adjustments to the sensitivity of the delta-peak
trigger can cure the glitch problem, although adequate screening
of the circuitry should be an equally valid solution.
Last
Modified: 16 Jan 2005 |