Triggering Circuits
There are three
main methods of triggering available. Firstly there is what is termed open loop
triggering. In this method the current is pulsed into the coil for a specific
period of time and then extinguished. Trial and error is used to determine the
best pulse period. This method encounters problems with its sensitivity to initial
conditions, in particular the projectile position. This method is perhaps best
used as a simple triggering system for a single coil where a user wants to experiment
over a range of pulse widths and projectile starting positions. An extension of
this method involves 'firing' a capacitor into a coil using an thyristor (SCR)
device. In this case the relative performance depends on the capacitor, coil and
projectile parameters.
Secondly we have
optical triggering. This type of system uses an infra red gate positioned at the
'input' end of the coil. As the projectile breaks the beam a signal triggers the
switching device. The device remains triggered until the projectile passes the
beam. Since we want the current to turn off just before the projectile passes
midpoint this places an upper limit on the length of the projectile. At most the
projectile length should be equal to the coil length.
Thirdly there is
induced voltage sensing. In this case a secondary sensing coil is wound round
the drive coil. This sensing coil detects flux linkage changes and produces a
voltage proportional to the rate of change of flux linkage. The induced voltage
can be used as a triggering signal.
The implementation
of these methods is described in more detail below:
1. Open Loop
Triggering -
We
will start by looking at a simple 555 timer circuit which can be configured to
produce a range of pulse outputs. In this circuit the 555 is said to operate in
'one-shot' mode. The timing behaviour of the 555 is governed by a resistor and
a capacitor. Take a look at the circuit in fig 1. In its non-triggered state the
output pin (3) is low and discharge pin (7) is low. In this state capacitor C1
remains discharged. When a negative edge is applied to the trigger pin (2) the
output goes high and the discharge pin goes into a floating state. C1 then begins
to charge and when the voltage at the threshold pin (6) reaches 2/3VCC
the output goes low. At this point pin (7) goes low and discharges C1. The device
is now in its reset state. Pins (4) and (5) are not used in the functionality
of this circuit. Pin (4) is the reset pin (active low). Pin (5) is the control
voltage pin which is decoupled via a capacitor to ground.
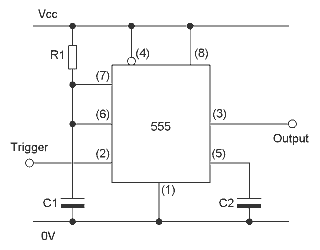
Fig
1.1
Now
the output pulse time tp is given by
This
equation arises from the time it takes the exponential RC transient to reach the
resetting voltage of 2/3 of the supply. If you solve the
general exponential growth function for a voltage of 2/3
max, the time solution will be 1.1 .
Note
that the LOW signal to the trigger pin on the 555 must be shorter in duration
than the output pulse width. You can make a trigger pulse circuit from common
digital components. An excellent source of circuits for timing applications is
Timer/Generator Circuits Manual by R.M. Marston.
2.
Optical Triggering -
This is a highly
versatile method since it provides precise triggering signals regardless of the
particular coil or energy supply configuration. It is also largely immune to electromagnetic
interference. The only possible pickup is in the wiring to the infra red gate.
It is however crucial that the gate is working correctly when main power is switched
on. If the optical gate fails then the switching device will be triggered and
voltage will be applied to the coil until it either burns out or the supply is
disconnected. Failure of the optical gate does not necessarily mean an electrical
failure, for instance if the emitter or sensor becomes blocked by dirt then the
system will produce a false trigger signal. The illustration below shows the physical
arrangement of the emitter and sensor. In this configuration the slots along either
side of the tube extend to the optical gate so that separate holes are not needed.
Fig
2.1
The
most basic circuit consists of an emitter-sensor pair, a switching device and
the coil. An improvement on the basic circuit involves some simple signal processing
with an opamp. To avoid confusion I'll call the gate 'clear' when the beam is
unbroken and 'blocked' when the beam is broken.
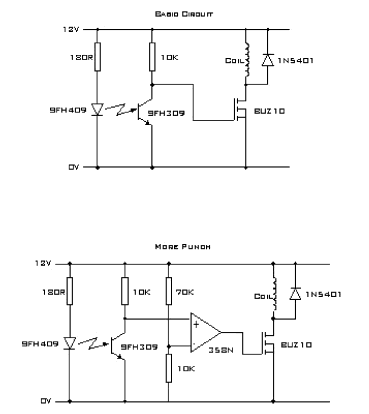
Fig
2.2
Let's
consider the basic circuit. When the gate is clear the phototransistor SFH309
is conducting and the voltage at its collector is small since most of the voltage
is dropped across the collector resistor. This is the voltage which controls the
switching device, a mosfet in this case. Now when the gate is blocked by the projectile
the phototransistor conducts very little current and so the voltage at its collector
rises closer to the supply voltage. This turns the mosfet on and current passes
through the drive coil. The projectile begins to accelerate into the coil and
as it approaches the middle of the coil it clears the gate. The phototransistor
now begins conducting again and the mosfet is turned off by the low collector
voltage. The diode across the drive coil is known as a commutating diode. Its
purpose is to reduce the voltage spike at the mosfet drain terminal when it switches
off. The theory section on switching devices explains the issues of switching
inductive loads.
The
second circuit is an improvement on the basic model. The opamp is being used as
a comparator and the sensitivity of the circuit can be adjusted by changing the
values in the resistor branch on the inverting input. The significant difference
is that the opamp output can source and sink considerably more current than the
phototransistor. This plays an important role when turning the mosfet on and off.
In order to turn on the mosfet you have to establish a voltage at its gate terminal
and this has a corresponding electrical charge associated with it. To turn off
the device this gate charge must be removed. How quickly the charge can be established
and removed dictates the switching speed. The opamp offers a current source/sink
of lesser resistance than the phototransistor and so it produces a faster turn
on/off.
3.
Induced Voltage Triggering -
This
sensing method seeks to make use of the dynamic magnetic flux associated with
the drive coil and projectile. If we look at the voltage induced in the sensing
coil we can see how this waveform can be used in a triggering circuit. The graph
below shows an induced voltage waveform. The trace resulted from turning on the
drive coil and letting the projectile oscillate back and forth in the tube. This
method is more suited to a constant voltage source supply since large transients
in the supply will cause problems with the definition of the turn off point. We
are only interested in the early part of the curve.
Fig
3.1
The
problem with implementing induced voltage triggering is that of tuning. The relationship
between induced voltage and projectile position depends on many interacting variables
so the setup will require some trial and error to achieve optimal trigger timing.
This is under development.
Last
Modified: 12 Feb 2004
|