Induced
Voltage Sensor
Delta-Peak
Trigger
Induced
voltage triggering is an alternative method of providing closed-loop
control of the coil current in single-stage or multi-stage transistor-fired
coilguns, or pseudo closed loop control of the current in multi-stage
thyristor-fired coilguns. The induced voltage trigger signal is
used to turn off the current on the active coil and initiate the
discharge through the next coil (if there is one). This is why it
is unsuitable for use with single stage thyristor fired coilguns
- the turn off functionality is superfluous. The main reason for
pursuing this method is that it should be possible to employ it
in very high power coilguns where the components of a directly integrated
optical trigger might be damaged by the intense, rapidly changing
field. That said, the optical trigger could be coupled to the coilgun
via fibre optic links, thereby eliminating the potential for device
damage, although this does add a layer of complexity.
Various
induced voltage sensor setups were designed and tested in order
to determine a suitable triggering point on the induced voltage
waveform. An optical trigger was incorporated into the test coils
so that this known turn off point could be used as a reference for
the induced voltage waveform. Initial designs attempted to minimise
the effect of flux linkage changes associated with the coil current
by utilising two closely spaced sensor coils connected such that
their voltages cancelled when the coil was dry fired. This approach
was based on two ideas; that the firing spike was an undesirable
signal feature, and the potential for external magnetic fields to
cause problems would be reduced by using closesly spaced sensors.
The
problem with this approach was that with the projectile located
at its launch position in the coil, the resulting asymmetry made
it very difficult to trim out the firing spike. The separation of
the sensors was also investigated but there was no waveform feature
close to the optical trigger turn off point that would be useful
for triggering purposes.
Fig
1 shows an example of a test coil* with closely spaced sensors positioned
centrally along the drive coil axis. The inclusion of the former
for holding the sensor windings significantly increases the inner
radius of the drive coil, thereby adversely affecting the performance.
Using a very fine wire would reduce the necessary radial displacement
but, as mentioned above, the lack of a suitable trigger feature
on the waveforms ended any further investigation of this design.
Fig
1. Dual sensor coil
At
this point it was decided that FEMM simulations would be a more
productive means of determining sensor voltage waveforms in relation
to projectile position. An example is outlined in Determining
Induced Voltage Signals Using FEMM.
Fig
2 shows the final design of the test coil based on results from
several FEMM simulations. An optical sensor is included for trigger
point verification and this forces the sensor coil to a location
where it triggers off the current earlier than the optical sensor.
Fig
2. General layout of functioning test coil.
Single
Stage Trigger Circuit
Referring
to the circuit of figure 3, let us consider the condition when the
circuit has just powered up:
The
op amps are DC biased such that the output of IC1b is low. The J-K
flip flop is configured such that positive transitions on the CLK
pin cause the Q output to flip state. The power up default for Q
is LOW. There are two capacitively coupled signal routes to the
CLK input of the flip flop which are isolated from each other by
signal diodes. The firing signal comes from a debounced microswitch
(the firing switch), and the turn off signal comes from the op amp
delta-peak detector. The delta-peak detector cannot trigger the
CLK pin while the Q output is LOW.
When
the microswitch is pressed:
The
output of the debounced logic goes HIGH and a short pulse appears
at the CLK pin. The Q output of the flip flop goes HIGH triggering
the switching device and initiating the capacitor discharge into
the drive coil. The negative induced voltage associated with increasing
sensor flux linkage (the firing / penetration spikes) is clamped
by the sensor signal rectifier diode. As the sensor flux linkage
begins to decrease due to the passage of the projectile, and to
a lesser extent, the natural decay of the coil current, the sensor
voltage becomes positive. The rate of change of flux linkage increases
to a maximum and then begins to decline as the rear of the projectile
passes the sensor, resulting in a voltage peak. A scaled analogue
of this maximum voltage is temporarily stored on C2 (the charge
decays through R1) such that the output of op amp IC1b goes HIGH
when the signal voltage drops slightly below its peak. The speed
of the output transition from IC1b is too slow to generate a sufficiently
short, capacitively coupled CLK pulse, therefore some logic gates
are employed to sharpen the edge, as well as provide 'sensor lockout'.
On receiving the second CLK pulse Q transitions to LOW and the switching
device is turned off. Note that since Q is now LOW, no further sensor
signals can toggle the flip flop.
This
dependency on the output state of Q is necessary in order to prevent
double triggering which can occur when the coil is turned off. Double
triggering is caused by a secondary sensor peak brought about by
the rapid increase in the di/dt decay rate
as the current is turned off. This secondary peak is detected and
results in Q being set HIGH again. Since the projectile has passed
the point of maximum rate of change of flux linkage there is no
further voltage peak from the sensor, therefore the capacitor completely
discharges into the coil.
The
use of this circuit is not limited to induced voltage sensors. Any
sensor that produces a falling edge at the point where the current
should be turned off can be used. It is possible to use an optical
sensor with this circuit where the output of the optical sensor
falls as the rear face of the projectile passes by.
Fig
4 shows a typical sensor signal with the coil current being controlled
by an optical trigger. The sensor peak occurs before the optical
trigger output falls resulting in what might+
be a premature turn off. The sensor position is limited by the inclusion
of the optical trigger, however there is no reason why the induced
voltage sensor cannot be positioned more favourably in a 'production'
coil. Note the occurrence of the second peak which coincides with
the coil current being turned off. This secondary peak occurs much
closer the primary peak when the current switching is controlled
by the delta-peak trigger.
It
is interesting to note that in fig 4 we see no distinction between
firing and
penetration spikes with this sensor setup. The main reason for
this is that the sensor used to generate the oscillogram in the
link above was located centrally along the coil axis. Since the
projectile takes some time to accelerate towards the sensor there
is a lag between the firing spike and penetration spike making them
distinct.
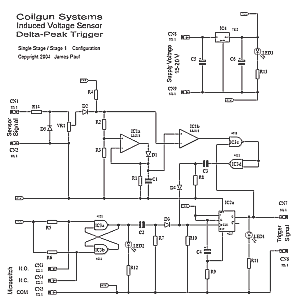
Fig
3. Delta-peak trigger circuit (click for large version)
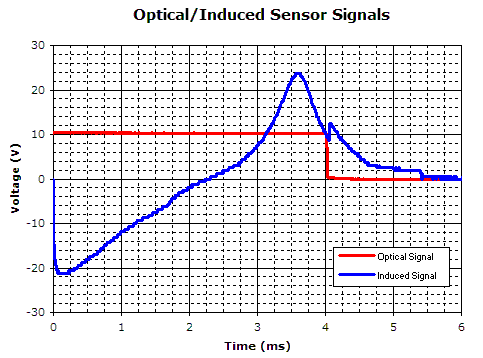
Fig
4. Induced voltage sensor signal showing secondary peak at turn
off.
Further investigation
will look into the cascading of trigger stages for use with multistage
coilguns.
*Note
the grooved region on the tube surface - this provides a good key
for the epoxy which fixes the formers to the tube. Previous designs
have used a simple roughened surface which has proven to be unreliable
over time.
+The
effect of the turn off point on velocity and efficiency has yet
to be investigated at the time of writing of this article.
Last
Modified: 12 FEB 2004
|