Electromagnetic Basics
1,2,3,4
14. Electromechanical Energy Conversion -
The core principles of electromechanical energy conversion apply to all electrical
machines and the coilgun is no exception. Before we consider the coilgun let's
imagine a simple linear electric 'motor' consisting of a stator field and an armature
immersed in the field. This is illustrated in fig 14.1. Note that in this simplified
analysis the voltage source and armature circuit have no inductance associated
with them. This means that the only induced voltage in the system is due to the
motion of the armature wrt to the magnetic induction.
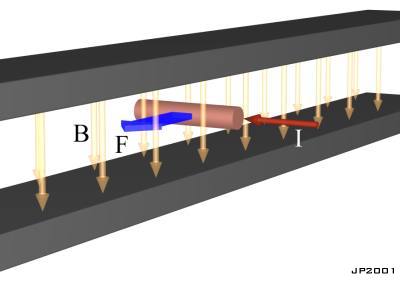
Fig 14.1. Primitive linear motor.
When a voltage is applied across the ends of the armature a current will be
developed according to its resistance. This current will experience a force (I
x B) causing the armature to accelerate. Now from the earlier section on electromagnetic
basics we illustrated the fact that a voltage is induced across a conductor
moving through a magnetic induction. This induced voltage acts in opposition to
the applied voltage (Lenz's Law). Fig 14.2 shows the equivalent circuit in which
electrical power is converted into thermal power, PT, and mechanical
power, PM.
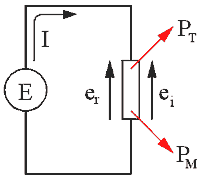
Fig 14.2. Motor equivalent circuit.
Now we need to look at how the mechanical power developed by the
armature relates to the electrical power supplied to it. Since the armature is
positioned at right angles to the field induction, the force is given by a simplified
version of eqn 11.4
so the instantaneous mechanical power is the product of the force
and velocity -
where v is the velocity of the armature. If we apply Kirchhoff's
voltage law around the circuit we get the following expression for the current,
I.
Now the induced voltage can be expressed as a function of the
armature velocity
Substituting eqn 14.4 into 14.3 yields
and substituting eqn 14.5 into 14.2 gives
Now let's look at the thermal power developed in the armature.
This is given by eqn 14.7
And finally we can express the power supplied to the armature
as
Notice also that the mechanical power (eqn 14.2) is equivalent
to the current, I, multiplied by the induced voltage (eqn 14.4).
We can plot these curves to show how the power supplied to the
armature is distributed over a range of speeds. In order for this analysis to
have some bearing on coilguns we'll give our variables values that are in keeping
with the coilgun pistol accelerator conditions. Our starting point is the current density
in the wire, from which we will determine values for the rest of the parameters.
The maximum current density during the coil testing was 90A/mm2 so
if we fix the wire length and diameter as -
l = 10 m
D = 1.5x10-3 m
then the wire resistance and current become -
R = 0.1 
I = 160 A
Now that we have values for resistance and current, we can specify the voltage
needed to drive the current -
V = 16 V
These are all the parameters required to plot the steady-state characteristics
of the motor.
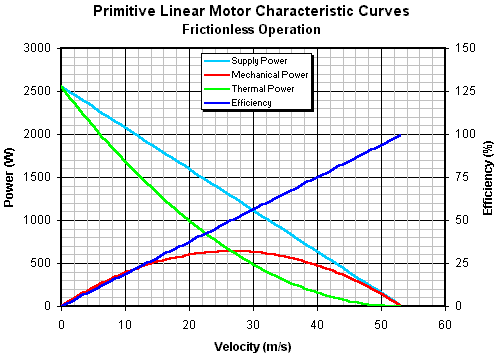
Fig 14.3 Characteristic curves for a frictionless
motor model.
We can make this model a bit more realistic by adding a constant
friction force, of say, 2 N, such that the mechanical power loss is proportional
to the armature velocity. This friction value is deliberately large to show its
effects more clearly. The new set of curves are shown in fig 14.4.
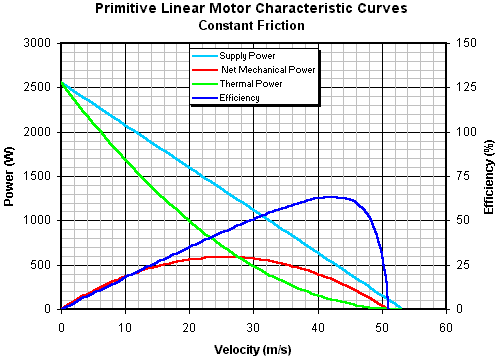
Fig 14.4. Characteristic curves with constant
friction.
The presence of friction slightly modifies the power curves such
that the maximum armature speed is slightly less the zero friction case. The most
striking difference is the change in the efficiency curve which now peaks and
then rapidly drops off as the armature approaches its 'no-load' speed. This form
of efficiency curve is typical of permanent magnet dc motors.
It's also worth looking at how the force, and hence acceleration,
varies with speed. If we substitute eqn 14.5 into eqn 14.1 we get an expression
for F in terms of v.
Plotting this expression we get the following graph -
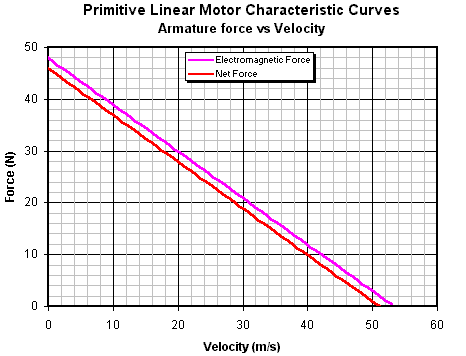
Fig 14.5. Armature force vs velocity
Clearly the armature starts off with a maximum acceleration force
that begins to decrease as soon as the armature starts moving. Although these
characteristics give a snapshot of the various operational parameters at any particular
speed, it would be useful to see how the motor behaves in time, i.e., dynamically.
|