Electromagnetic Basics
1,2,3,4
14. Electromechanical
Energy Conversion -
The dynamic response
of the motor can be determined by solving the differential equation which governs
its behaviour. Fig 14.6 shows the free body diagram of the armature from which
we can determine the net force and then write the differential equation.
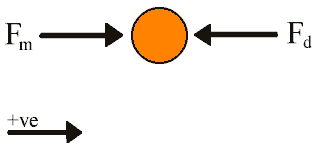
Fig
14.6 Armature free body diagram
Fm
and Fd are the magnetic and drag forces respectively. Since the voltage
is a constant we can use eqn 14.1 and the net force, Fa, on the armature
is
We
can now write an expression for the acceleration of the armature
If
we write the acceleration and velocity terms as derivatives of displacement, x,
wrt time, and rearrange the expression we get the differential equation for the
motion of the armature
This
is a second order nonhomogeneous equation with constant coefficients, and it can
be solved by determining the complementary function and the particular integral.
The solution method is straight forward (any college level maths text will cover
differential equations) so I'll just present the result. One point to note is
that this particular solution uses the initial conditions: x = 0, dx/dt = 0.
We
need to assign values to the friction, magnetic induction, and armature mass.
As far as friction is concerned, I'll just use a value of 2N to illustrate how
it affects the motor's dynamic characteristics. Determining a value for the induction,
that will produce a similar accelerating force in the model as it does in the
test coils for a given current density, requires that we look at the radial component
of the flux density distribution coming out of a magnetised coilgun projectile
(it's the radial component which develops an axial force). This is integrated
over the volume occupied by the coil and a force expression is generated by multiplying
this by the current density, J, and filling factor, F. The expression is then
equated to BIL for our model and Bmodel is obtained by solving equation
14.15, where is
the wire diameter.
We
can look at the magnetic flux from a magnetised projectile (without a coil current)
as shown in fig 14.7.
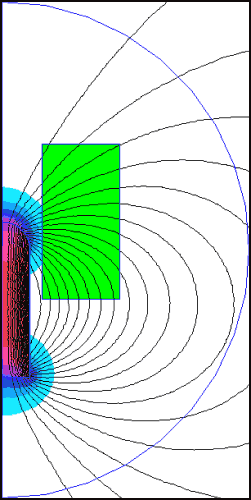
Fig
14.7. Determining volume integral of radial flux density using FEMM
The
projectile is 'magnetised' by giving it a B-H curve and an Hc value in the FEMM
material properties dialog. Values were chosen to resemble strongly magnetised
iron. FEMM gives a value of 6.74x10-7 Tm3 for the flux density
volume integral Bcoil, so using F = /4
we arrive at Bmodel = 3.0x10-2 T. This flux density value
may seem very small considering the flux density inside the projectile is around
1.2T, however, we must realise that the flux expands into the much greater volume
around the projectile with only a fraction of the flux resolves to a radial component.
Now, you'll realise that, compared to our model, a coilgun is 'inside out' and
'back to front', in other words in a coilgun the stationary copper surrounds a
magnetised part which moves. This is no problem though, the essence of the system
is the paired co-linear forces acting on the stator and armature so we can 'fix'
the copper part and allow the stator field generator to move instead. Since the
stator field generator is acting as our projectile it will have a mass of 12 g
assigned to it.
We
can now plot the displacement and velocity as functions of time as shown in fig
14.8
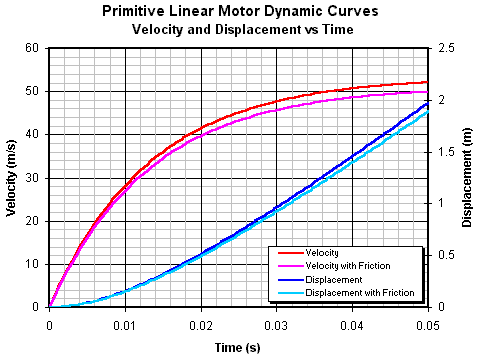
Fig
14.8. Dynamic behaviour of the linear motor.
We
can also combine the velocity and displacement equations to give a velocity vs
displacement function as shown in fig 14.9.
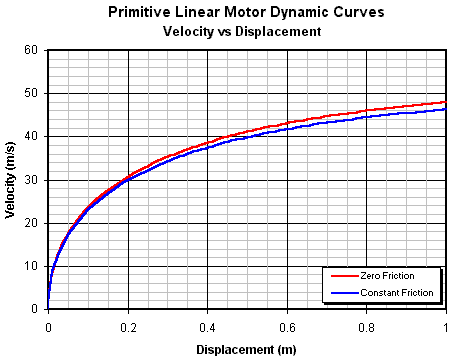
Fig
14.9. Velocity vs displacement characteristics.
The
important thing to notice here is that a relatively long accelerator is needed
before the armature begins to reach its maximum speed. This has implications for
the maximum efficiency of a practical accelerator.
If
we zoom in on the curves we can see what velocity is achieved over a length equal
to the length of the active material in the coilgun pistol accelerator coils (78 mm
total).
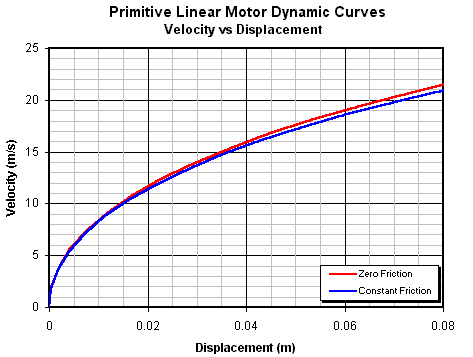
Fig
14.10. Close up of velocity vs displacement curves.
This
is surprisingly close to the actual performance of the three stage pistol accelerator,
however, this is just a coincidence since there are several significant differences
between this model and an actual coilgun - eg in the coilgun the force is a function
of the velocity and displacement coordinates whereas, in the present model, the
force is only a function of the velocity coordinate.
Fig
14.11 is a plot of the cumulative efficiency of the motor as the projectile accelerates.
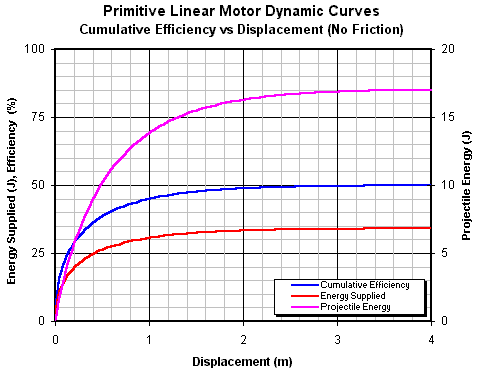
Fig
14.11. Cumulative efficiency as a function of displacement with no friction losses.
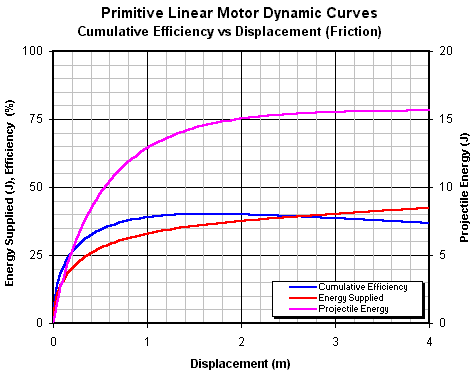
Fig
14.11. Cumulative efficiency as a function of displacement with constant friction
losses.
The
cumulative efficiency illustrates a fundamental property of this type of electrical
machine model - the energy gained by the armature when it accelerates from rest
up to its no-load speed is exactly half the total energy supplied to the machine.
In other words, the maximum possible efficiency of an ideal (frictionless) accelerator
fired by a step voltage is 50%. If friction is present then the cumulative efficiency
exhibits a maxima turning point caused by the machine doing work against the friction.
Finally,
let's look at the effect of B on the velocity-displacement dynamics as shown in
figs 14.10 and 14.11.
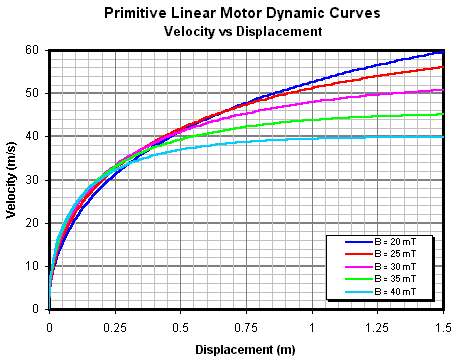
Fig
14.11. Effect of B on velocity-displacement gradient.
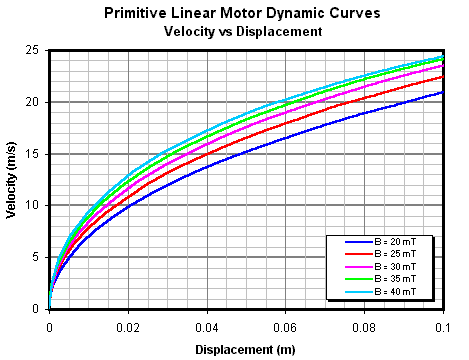
Fig
14.12. Small displacement region where increasing induction yields a greater velocity.
These
curve sets show an interesting property of this model in which a larger field
induction initially yields a higher velocity over a given displacement, but as
the velocity increases the lower induction curves 'overtake' those representing
stronger induction. This makes sense when you consider that the stronger induction
will yield a greater initial acceleration, however, the correspondingly larger
induced voltage causes the acceleration to decrease more rapidly allowing the
lower induction curves to 'catch up'.
So,
what can we learn from this model? I think the important thing to realise is that,
starting from standstill, the efficiency of such a motor is going to be quite
low, especially if the motor is short. The instantaneous efficiency increases
as the projectile gains speed due to the induced voltage reducing the current.
This increases the efficiency because the resistive power loss is dropping while
the mechanical power is increasing (see figs 14.3, 14.4), however, since the acceleration
is also dropping it takes progressively more displacement to make use of the improving
efficiency. In short, a linear motor subjected to a step voltage 'forcing function'
is going to be quite an inefficient machine unless it is very long.
This
model of a primitive motor is instructive in that it points to the cause of the
typically poor efficiency of coilguns - namely a low motion-induced voltage. The
model is oversimplified as it takes no account of the nonlinearities and inductance
elements of a practical system, so to refine the model we need to incorporate
these elements into our electrical circuit model. The next section will develop
a generalised differential equation for a single stage coilgun. The analysis will
attempt to derive an equation which can be solved analytically (some simplification
will be needed), failing that, I'll need to use a Runge Kutta numerical integration
algorithm.
Sources:
Introduction to
Magnetism and Magnetic Materials, David Jiles
Electromagnetics
(Schaum's Outline Series), J.A. Edminister
Introduction to
Electromagnetism, M. Sibley
Principles of Electromechanical
Energy Conversion, J. Meisel
University Physics,
Harris Benson
Introductory Circuit
Analysis, Boylestad
|