Enhanced Flux Linkage
Experiments
Enhancing
the Flux Linkage -
The
reason for enhancing the flux linkage is that it improves efficiency
by increasing the force and therefore work done on the projectile
for a given coil current. In order to increase the flux linkage
we need to increase the permeability of the path along which the
flux 'flows'. This is done by introducing a ferromagnetic material
such as iron or electrical steel into the air space around the coil.
Fig 1a shows the three configurations that are compared in these
experiments. Fig 1b and 1c show the results of magnetostatic FEMM
simulations in which the coil current is fixed and 1006 carbon steel
is introduced into the flux path. The current density used to generate
the results of fig 1c is twice that of 1b.
The
projectile is a mild-steel right-cylinder with a length of 25 mm
and a diameter of 9.4 mm. The coil dimensions were set as outlined
in table 1.
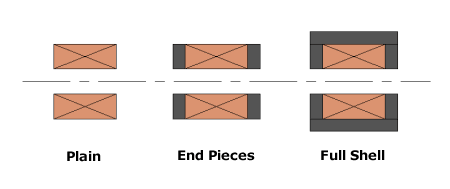
Fig
1a. Addition of flux path enhancement.
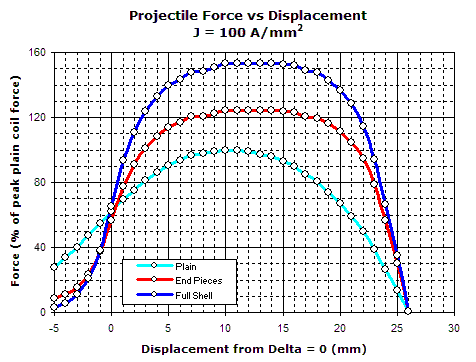
Fig
1b. Force curves for flux enhancement configurations.
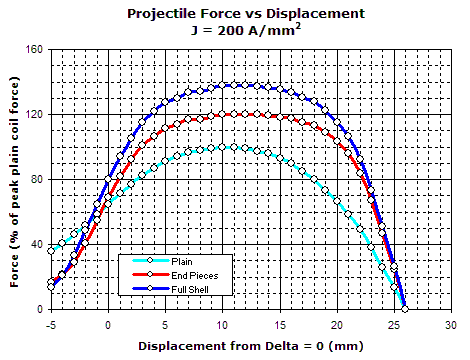
Fig
1c. Force curves for flux enhancement configurations.
Length |
Ro |
Ri |
|
Turns |
Res |
Ind |
27 |
18 |
7 |
1.8 |
~70 |
~40
m |
~
uH |
Table
1. Coil parameters.
Clearly
the addition of flux path enhancement causes a large increase in
the peak force, accompanied by a flattening of the force curve.
It is interesting to note the proportional reduction in force enhancement
when the current density is increased. This can be attributed to
the reduced permeability as the shell material gets closer to saturation.
Two
other noteworthy features of these curves are: firstly, the plain
coil force exceeds that of the flux-enhanced versions as delta becomes
negative; and secondly, the gradient of the force curve is much
steeper at the midpoint for flux-enhanced coils. The first point
suggests that velocity will be more sensitive to negative values
of launch delta with flux-enhanced coils. The second feature points
to the likelihood of increased turn off sensitivity with the flux
enhanced coilguns since suckback may become more dominant.
The
shell needs to be formed from either a laminated or powdered material
so as to minimise eddy currents and thus allow rapid diffusion of
the field into the shell. A laminated structure formed from mains
transformer leaves has been investigated by Barry(1).
It was decided that a simple comparative investigation between a
plain coil and a powdered-iron flux-enhanced coil should be undertaken.
The use of powdered iron allows for the construction of a shell
of any desired shape, within the limits of basic moulding and machining
processes.
Making
The Shell -
The
shell was designed as three distinct parts; two end pieces and a
sleeve. The sleeve fits over the end pieces forming the complete
shell. The shell material is a mixture of potting epoxy and iron
powder with a maximum particle size of 450 um. The moulds for the
end pieces and sleeve are made from nylon 66. The moulds, moulded
parts, and completed flux enhanced coilgun are shown in figs 2a
- 2k (click for larger image).
The
mould mixture was prepared by adding epoxy to a quantity of iron
powder until the mixture had the consistency of a moist paste. The
mixture was then introduced into the mould in small quantities and
lightly packed with the end of a dowel. When the mould was filled
to the desired level the lid was fitted and the compression nut
tightened as much as possible. Due to the limited compression forces
that can be applied in a nylon mould the resulting percentage of
iron in the epoxy matrix was only about 60 % by mass. The mixture
was allowed to cure for a period of 48 hrs before removing the parts.
The
bore of each end piece was turned to the diameter of the stainless
steel tube, with one of the end pieces modified to accept both optical
and induced voltage sensors (latter not used in these experiments),
and then epoxied in place. After an appropriate curing period the
assembly was turned in the lathe to produce an accurate diameter
on the end pieces. The bore diameter of the shell was turned to
produce a snug fit over the end pieces and cutouts were formed to
allow access for the coil wiring and optical sensors.
No
attempt has been made to characterise the magnetic properties of
this material as this will be investigated when a more effective
moulding system is developed.
Experiment
-
Three
coilgun configurations were tested; a plain coil, a coil with iron
powder end pieces, and a coil with a full iron-powder shell. The
triggering system was an optical gate combined with a delta-peak
trigger to allow for variation in the launch delta. The switch
comprised a set of 8 IRF3415 MOSFETs connected in parallel and an
MC34152 MOSFET driver. A series connection of ten 1N5402 rectifier
diodes were used to ramp down the coil current at turn off. No resistive
current sensor was employed during these experiments as this is
slightly detrimental to efficiency.
Six
sets of experimental runs were conducted as outlined in table 2.
Two speed trap values were taken for each launch delta. The remaining
voltage on the capacitor was also recorded.
Experiment |
Configuration |
Capacitor
(uF) |
Voltage
Range |
Delta
Range |
1 |
Plain
Coil |
13,600 |
50
to 100 (x10 V) |
-5
to 12 (x1 mm)
|
2 |
Plain
Coil |
33,000 |
30
to 60 (x5 V) |
3 |
End
Pieces |
13,600 |
50
to 100 (x10 V) |
4 |
End
Pieces |
33,000 |
30
to 60 (x5 V) |
5 |
Full
Shell |
13,600 |
50
to 100 (x10 V) |
6 |
Full
Shell |
33,000 |
30
to 60 (x5 V) |
Table
2.
Results
and Conclusions
(1)
Coilgun Mark
III
Last
Modified: 30 Mar 2004
|